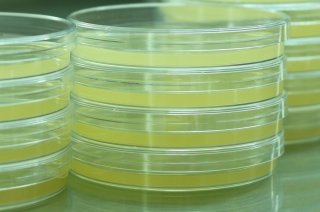
category_news
Ourobionics: Tissues with biosensors for medical research
Since 2021, Ourobionics has had an office in the Plus Ultra II building, where computer, microscope and 3D printer are now located side by side. In the future, the company hopes to produce human and animal tissues on a large scale for medical research. A recent investment from the East Netherlands 'ION+2 fund' will allow Ourobionics to accelerate its plans. In conversation with co-founder John Zandbergen.
Why are you developing tissue cultures?
"The rules on animal testing are becoming increasingly strict in Europe, for cosmetic purposes but also for medical research. Animal research is also inefficient because the results often do not translate to humans. Our aim is a world in which animal testing is no longer needed at all. However, this does require much better alternatives than are currently available. Tissue cultures and organoids (artificially grown miniature organs) may be becoming increasingly complex, but who says they mimic the functioning of an organ well enough?"
So how are the models you develop different from regular tissue cultures?
"We combine complex tissue cultures with innovative technology. The term bionics in our name also refers to the merging of biology and technology. The two professors from England and Denmark who started this are now our scientific advisers. We use a 3D printer to make tissue models with different materials, cells and biosensors. We can then measure what is happening in the tissues."
What kinds of sensors are involved?
"In such a model, we measure general values, like pH and temperature, as well as specific disease indicators, also called biomarkers. For example, one of our sensors measures the hormone dopamine. We need this sensor for a brain model of Parkinson's disease. For different diseases, we want to develop models with their own specific sensors. We will start with models for skin diseases and then other diseases."
What is the biggest challenge in developing your models?
"Making tissue cultures has always involved a lot of manual work. That makes it almost impossible to supply hundreds or thousands of the same copies of a model. However, companies in the medical or cosmetics industry need that for their testing. By 3D printing and further standardising the production process, we are trying to make increasingly uniform models. That remains the biggest challenge."
Why did you choose Wageningen Campus as a base?
"It was no coincidence that we started looking in this region. That was also a requirement of the Eastern Netherlands ION+2 fund. When we arrived on campus, we immediately loved it. Plus Ultra II is a lovely modern building. It is very inspiring to be among so many start-ups. And we can share laboratory facilities and collaborate with large companies here on campus."
Do you work with the University?
"We are in talks with the Animal Sciences Group. They do animal testing there too, but with the same mission to find good alternatives. So, the obvious way forward is to collaborate with ASG research groups. Our technology is equally well suited to developing animal tissue models too.
Furthermore, a couple of students will be doing some market research for us in the coming months. We know that companies are interested in our skin models, but we want to know more about which tests they need models for. That is an important question. In one or two years, we expect to start producing on a large scale. Then we need to know exactly what the market wants."
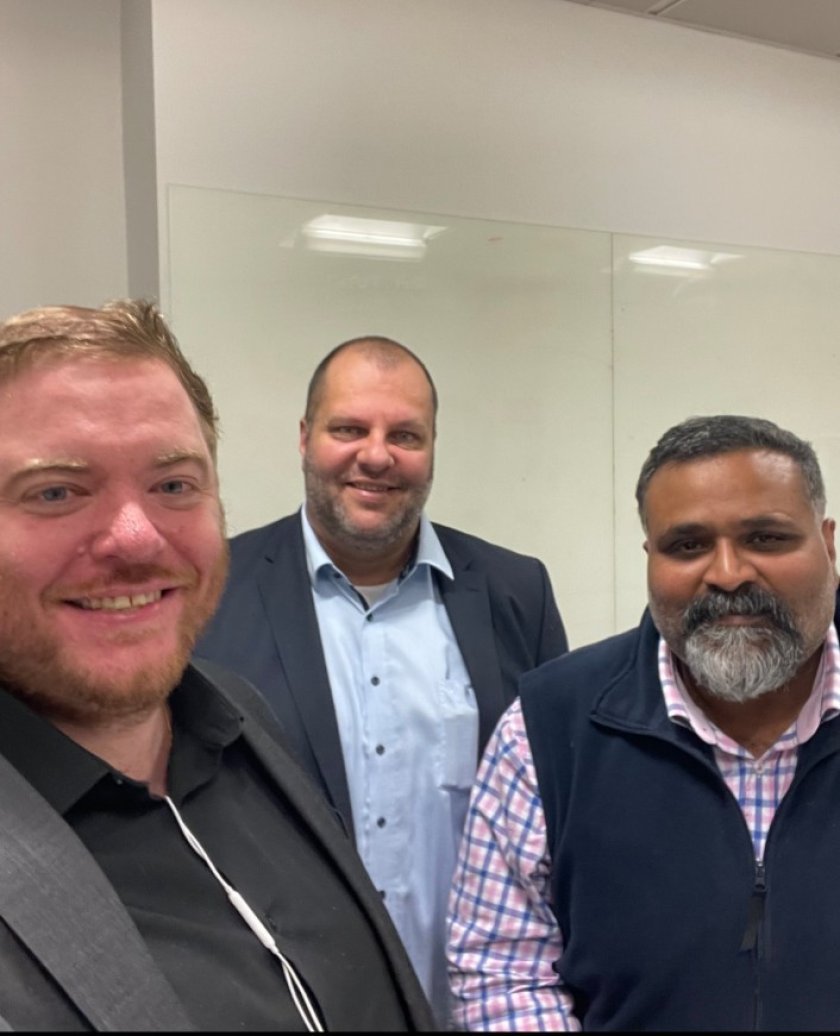